Here's a blow-by-blow of making the cartridges for the .50 Alaskan
Below you will find the steps I use to make my .50 Alaskan ammo starting with .348 Winchester cases and cast bullets. The processes, in general, are applicable to any cartridge, be it wildcat or obsolete, that one would like to make starting with another case.
The first photo is of the .348 Win case marked to length, trimmed to length, and the resulting .50 case.

The second photo shows trimming the .348 case to length. I removed the shaft from a manual case trimmer and chucked it in a 1/2" power auger. There's lotsa metal to remove to get the case to proper length.

The next step is to remove the burrs - both inside and out - caused by trimming the case.
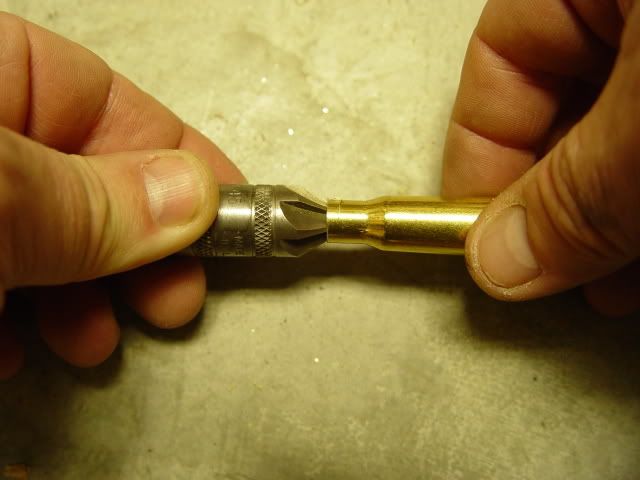
Since this case is going to get blown out essentially straight, the shoulder and neck get annealed first to soften them up as much as possible. I hold the case between my index finger and thumb while I am annealing. When the case gets too hot to hold onto, I drop it. I used to drop it in water, but it seems to me that that might just harden it a bit. I've been told by an internet metalurgist that brass does not "temper quench" like iron/steel does. Still... I'm certain it doesn't harden with air cooling.

Here's what the annealed case looks like.

After I have annealed all of the cases I intend to fireform, I charge them. You can see the components in this image. They are: About 15 grains of Bullseye; enough Cream of Wheat to fill the case about half way up the neck; and some paper towel for wadding. I put a piece of paper towel between the powder and the CoW just so there is no chance for the powder to get mixed with the CoW. Once the CoW is added, I put a wad of paper towel on top and tamp it down just so the CoW doesn't pour out the case mouth.

Here are the powder-charged cases:
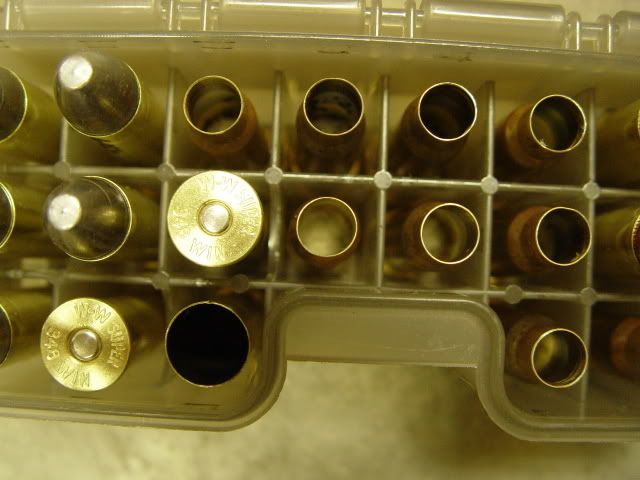
Here are the CoW-charged cases:
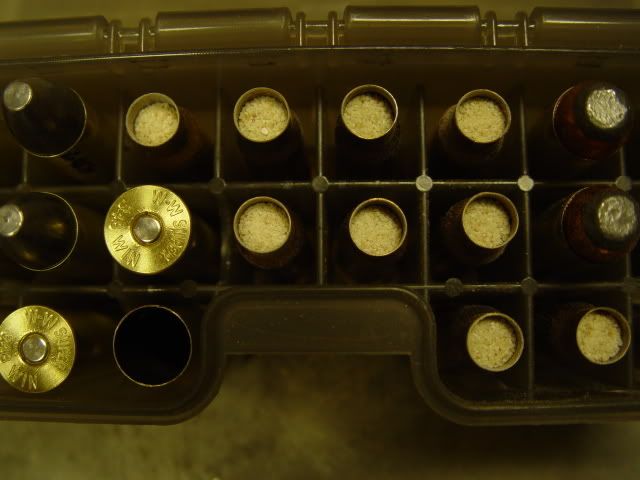
And here are the cases ready to be fire-formed:

Here are the cases immediately after fire-forming. So far I've done this with 100 cases. Only one has split, and that one wasn't annealed. I fire-formed 40 cases before I started annealing, and only one split. Still, annealing is too easy to do, and even if it only saves 1% of the cases, it's still worth it to me.
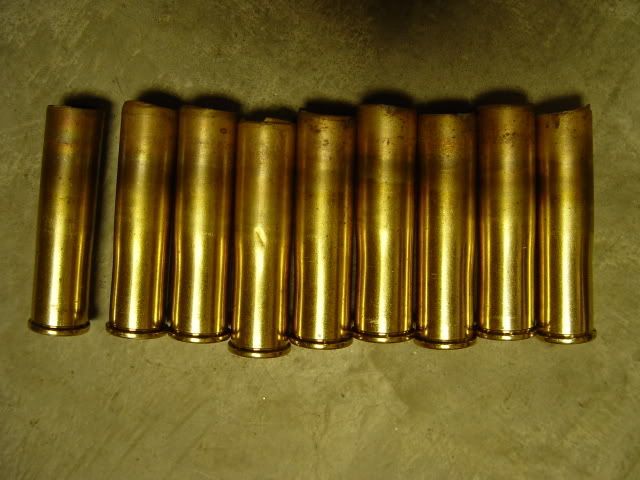
After fire-forming, the mouths are very uneven and need to be filed square. I tried to use the case trimmer, Brithunter even made a custom pilot for me. However, the cutter is just too small for the fire-formed case mouth. Filing isn't too tedious - at least not to me.
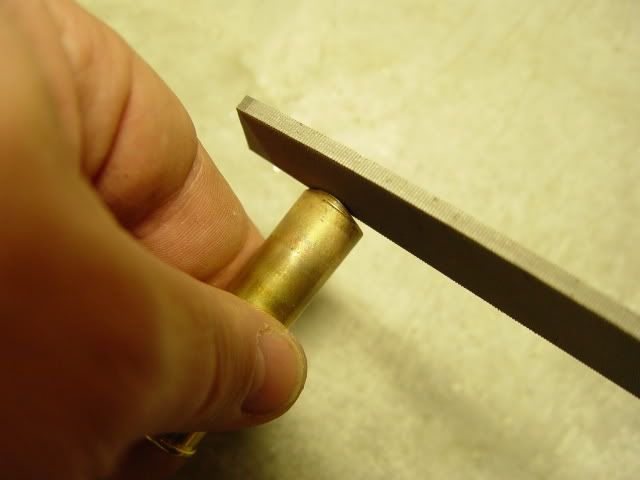
After squaring the mouth, I remove the burr inside and out and chamfer.
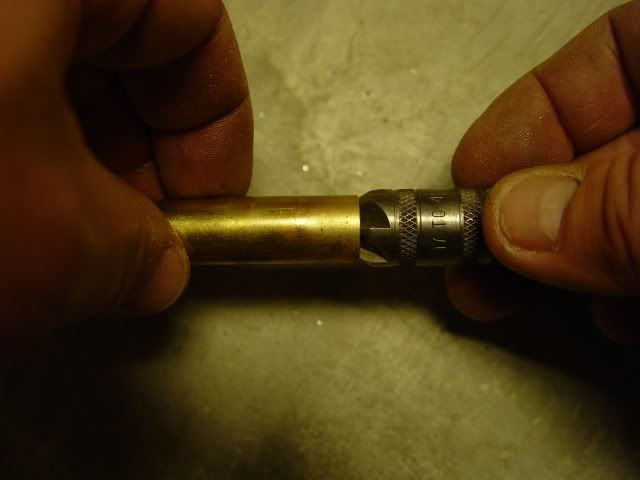
Next, I like to polish the cases. On one hand it's purely cosmetic. On the other hand, I can see any flaws better on a polished case. I polish the cases by using something wooden lathe turners will be familiar with - a jam chuck. I make the jam chick from an 8mm Mag case. The .50 case gets jammed on the 8mm case and spun. I use an artificial abrassive pad that is fine enough that it just polishes. Here is the polishing process in pictures:



Now that the case is made, it's time to make the bullets. I'll spare you the casting process, and start out with the cast bullets in hand. These are bullets dropped from Lee's 450'grain mould. With my alloy, they turn out 439 grains.

Notice that they have no gas-check heel. Try as I might, I have been unable to get un-gas-checked bullets to leave no lead in my bore. Put another way, bullets without gas-checks SERIOUSLY lead the bore of my rifle. I'm sure some casting guru could make an alloy that wouldn't lead, but I am simply not capable of doing so. So, I need to put a gas check heel on these bullets. Another GBO fellow came to my aid. Drinksgin made a little lathe for cutting gas checks in non-gas-checked bullets. (Don is quite a 'fixer'.)
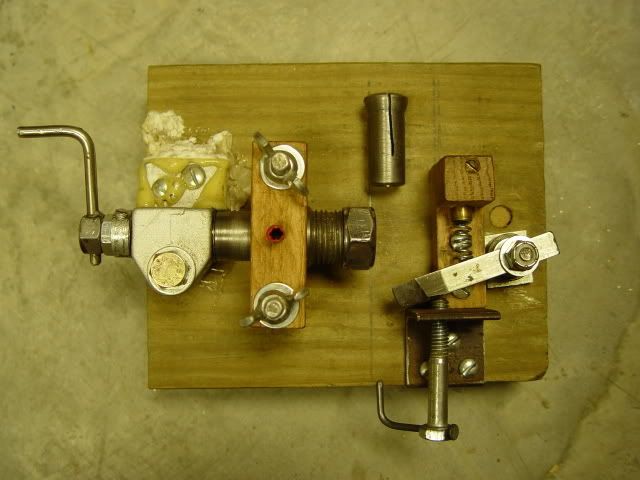
Here is the lathe in operation:
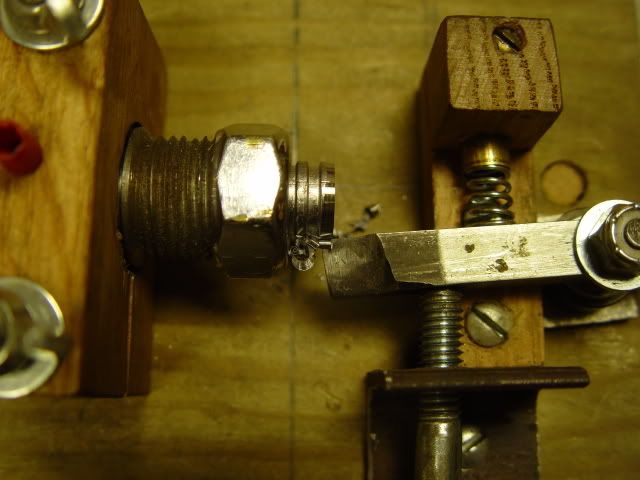
Here is the result with gas check along side:

And here is the finished product.

Now it's time to lube the bullet. Again a THL member comes to my aid. Jay Edwards gave me some of his special lube to use in addition to the gas check, to try and alleviate the leading problem. Here are the GC'd bullets sitting in the melted lube.

Here they have cooled, and along side is a removal die I made by fire-forming a 7.62x54R case to the .50 Alaskan chamber. (It didn't blow the head out enough to use as a suitable case for making .50 Alaskan cases.)

The next two pictures show the die in place and the bullet in the die after removal from the lube.
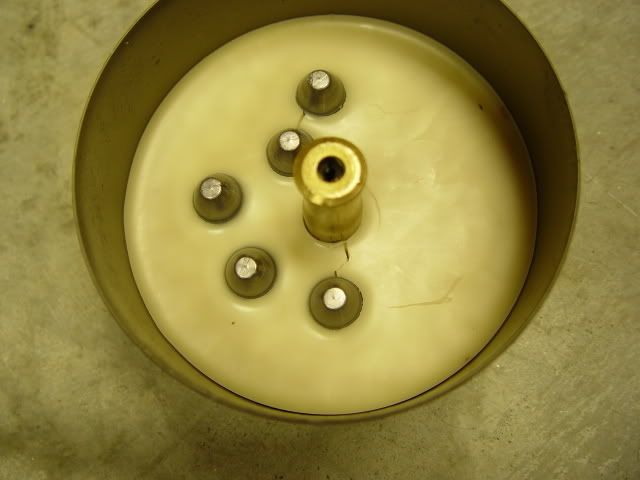

These are the lubed bullets.
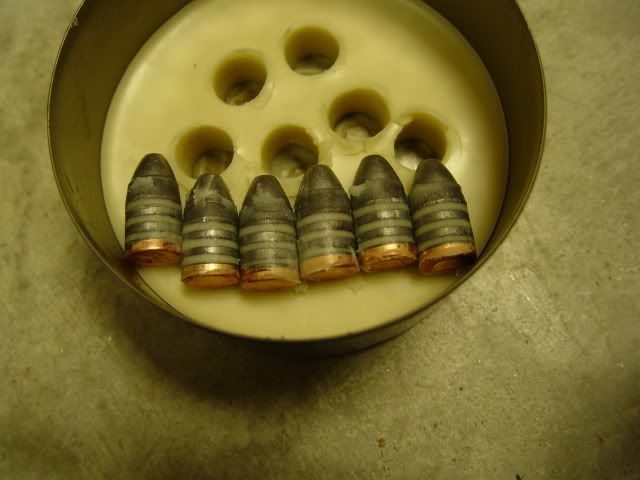
And here is a loaded .50 Alaskan cartridge.
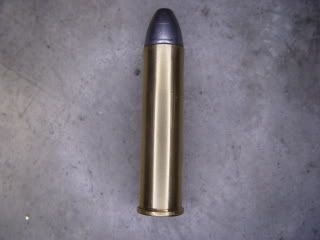
So... if you wanna make your own wildcat, be prepared to spend a little time in 'other' activities. There are easier ways however. You could simply buy the .50 Alaskan cases at ~$1.00 apiece, and load them with Barnes' 450-grain .510 Original bullets. Or... you could buy already-loaded-ammo at $5.00 a piece.

As for me, I enjoy makin' 'em from scratch.
Paul