Here is a long photo story about how to make a fiberglass stock for a single shot rifle (Thompson-Center TCR-87). This was about 80 hours work for me.
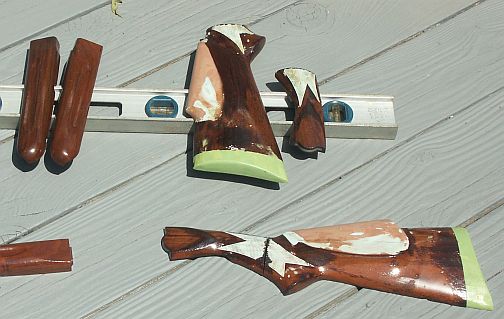
Above: First I had a beatup old wood stock with too much drop so I added a cheek-piece of body putty and added to its short pull with body putty. I then had a friend cut both the buttstock and forend in two, lengthwise. These pieces wood serve to make molds for the fiberglass stock.
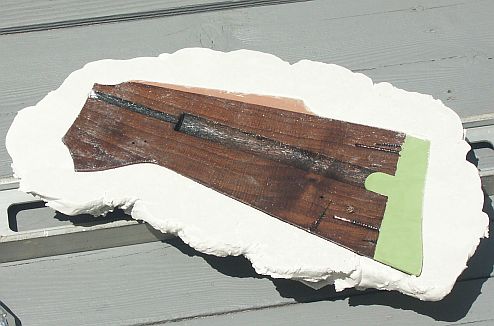
Above: The pistol grip areas and the rear areas of the buttstock were formed separatley. Here is a rear portion of the wood buttstock still in the plaster-of-paris mold.
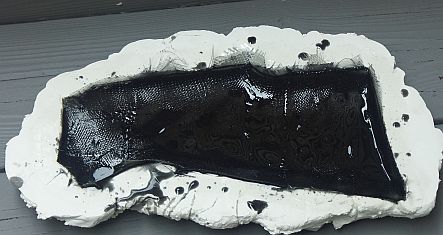
Above: Here is the mold with some fiberglass cloth and epoxy in it. More and more layers were added and sometimes I changed coloring to better keep track of thickness.
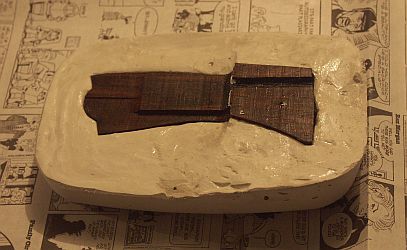
Above: Like with the rear parts of the buttstock, I started by making a one-piece mold. Here it is with the wood in it.
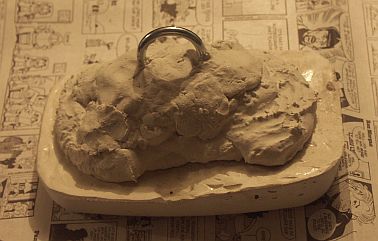
Above: Different from the rear part of the buttstock, the pistol grip areas required two-piece molds. This is the other half of the mold attached to the first part. I built up layers of glass in each part of the mold so the surfaces would be strong from the fiber. Then I put the two halves of the mold together and injected epoxy within. The "in" hole for the epoxy and the "out" hole to bleed out air don't show up here. I used a shringe to inject the epoxy.
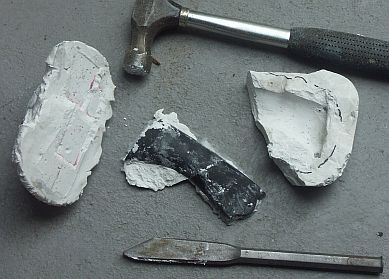
Above: It was impossible to get fiberglass parts out of the molds without damaging the plaster-of-paris molds. I ended up just trying to save the molds and broke them to get the fiberglass parts.
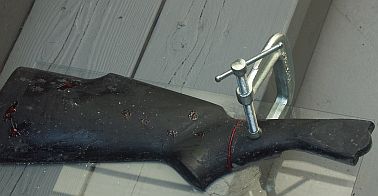
Above: Here I made an initial attachment of the pistol grip and rear portions of the buttstock. This was not a final joint as it needed glass fiber added for strength.
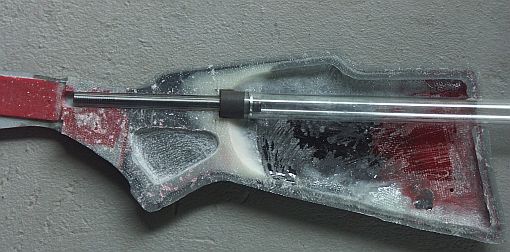
Above: I had to add solid material into the inside of the stock for strength and provide a channel for the bolt used to attach the stock to the action. There were lots of small steps here to be sure the bolt hole would not fill up with epoxy.
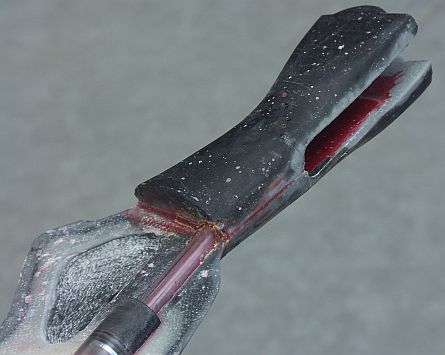
Above: Once I got the other half of the pistol grip attached and both sides bedded to the action it seemed like progress was being made.
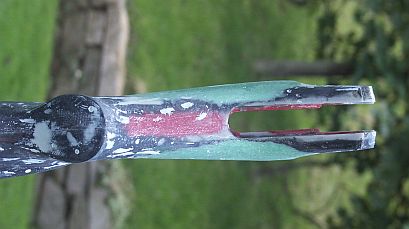
Above: I finally got the rear part of the buttstock attached to the rest of the butstock. Then I had to cut many channels into the parts so I could make lots of glass fiber and epoxy straps to join there with better joints. This photo shows where I added thickness in the pistol grip area compared to the factory stocks (green color). I wanted to be sure it would not break under recoil. With a .50-140 Sharps barrel it is possible to get about 90 foot-pounds of recoil energy. Between shooting with the .50-140 barrel and a 10-gauge magnum barrel one of the factory stocks had split in the pistol grip area.
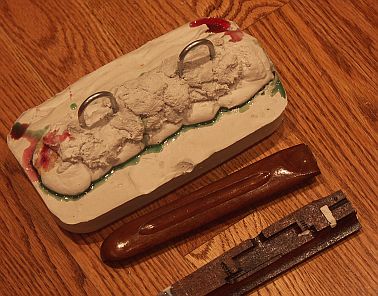
Above: Here is a two-piece mold for half the forend. I added very little glass cloth in the forend parts as they did not need so much strength as the pistol grip and buttstock.
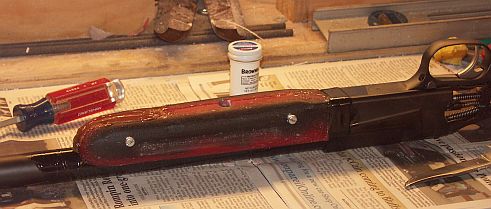
Above: It took a while to get the forend parts bedded to the barrel hanger hardware and front of the action. The trick was to take small steps to be sure everything did not end up getting glued together.

Above: After a lot of sanding and adding a recoil pad I decided to hire a professional stockmaker to do the final painting. This stock was built heavy-duty to stand the recoil of the .50-140 and 10-gauge barrels. It weighs about the same as a wood stock, but the balance is farther forward and higher up than a wood stock. If I make another stock it will be much lighter as a Thompson-Center TCR-87 action is very light. With a light stock, a factory light barrel, and a small scope it would make a very light rifle.