:evil: :cry: it was 1/8 evil little drill bit, bran spanking new,
tried to drill beside it, snapped that one too,evils little twin,
,,now theres two,stuk,broken bitts laughing at me

,or WAS,,,
ive wrecked, sacraficed, two 1/4 bitts, and 3, 1/4 inch end mills,
i dipped them in distilled water, :lol:
but i now have a CLEAN, WOPPING, .366 HOLE,
with the top 1/4 looking like crap,
you can see the burnt wood on the tail end, the wife came running in with the fire extinguser, and im stand ing there watching the torch,
shes screaming im on fire, i said,,,yup, leter burn,,,, :-D
she put my son on guard duty,,,,
is a 3/8 fuse hole too big?
im thinking ofHeat/freeze- presure fitting a piece turned on the lathe,
1/4 taller than the cannon, then welding in all the GAP,
and grinding it smooth,
,
please let me know if this would be safe,
thanks Guys, good to know you all are there,
im taking a valium, and taking the rest of the night off,,,, :-D,
and half a day tommorrow, maybe saterday, probably sunday,
,
johnp
Have i ever mentioned i hate drilling small holes,
:-D
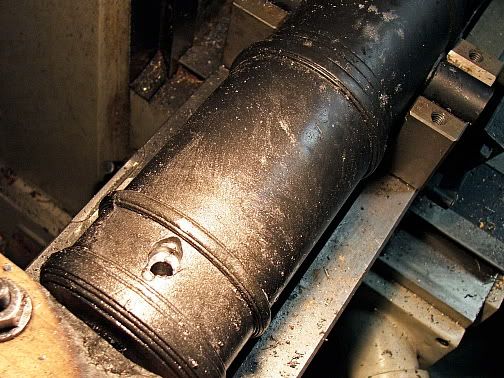
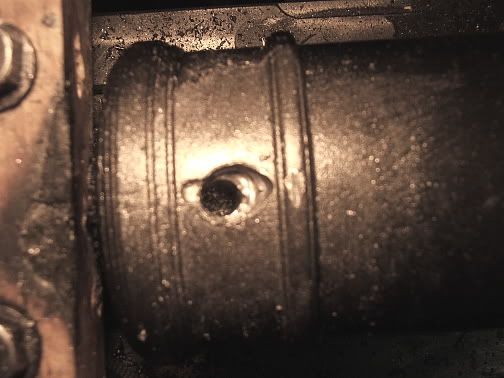